由于钣金折弯成形零件具有结构紧凑、质量轻巧、承载能力大、加工简单和生产效率高等优点,其在机车车体、转向架等骨架上得到了越来越广泛的应用。数控折弯工艺采用间隙成形,且具有各种不同开口角度模具,可以得到精度很高的各种复杂压型零件,具有传统的压力成形工艺无可比拟的优势。采用该工艺不再需要针对不同规格的压型件设计专用的配套模具,能够满足产品种类多、更新快、新产品试制周期短的要求。因此,拥有一套成熟的数控折弯成形工艺,可以为新项目的快速投产、新车型的开发、新设计思想的贯彻提供充分的保障。
工艺参数的选择与确定
对于钣金件的数控成形,工艺参数一般需要从以下几个方面进行考虑。
展开尺寸的计算
中性层的位置不仅与弯曲半径、板厚、中性层内移系数等有关,而且还与弯曲方法、模具结构、弯曲件形状及其尺寸标注等多种因素有关。因此,压型件中性层的位置是无法精确确定的。实际应用中一般采取近似值计算。
传统展开尺寸L的计算公式为L=a+b+l(见图1)。式中,a,b为直线段;r为弯板内弧半径;l为圆弧段长,l=π(180°-β)(r+tk)/180°,式中,t为钢板厚度,β为张角,k为中性层系数,其具体取值参照表1。
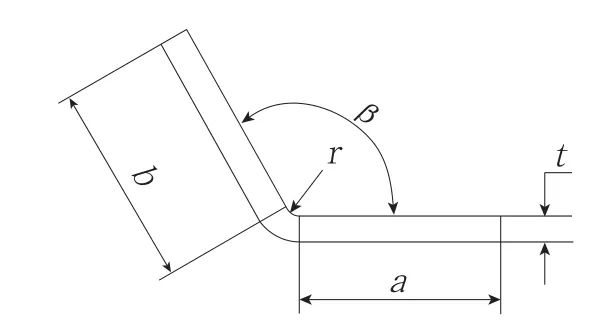
图1 角形件传统标注
表1 中性层位置系数k的值

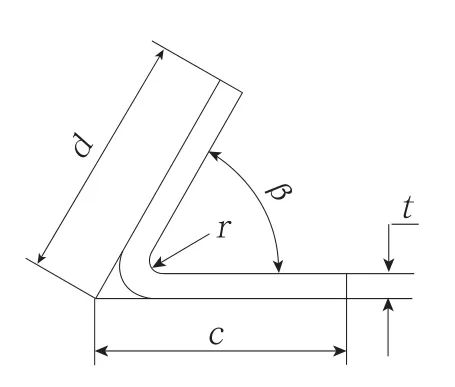
图2 角形件尖角标注
设计图纸常采用尖角标注(图2),为了便于计算,我们推出了以下展开计算公式:L=c+d+v,式中,v为补偿值,β=0°~90°时,v=π(180°-β/180°) (r+2tk)-2(r+t);β=90°~165°时,v=π(180°-β/180°)(r+tk)-2(r+t)tan[(180°-β)/2];当β=90°时,v=(1.57k-2)t-0.43r;当165°<β<180°时,v=0,L=c+d。从近几年的反复验证来看,一般情况采用该公式计算的展开料精度能满足设计要求。
折弯模具的选用
数控折弯采用间隙折弯工艺,不管板料的厚度如何,其内弧半径约等于模具开口距的0.156倍,这是床的固有折弯半径。只有当上模半径大于机床固有半径时,所得折弯件的内弧半径才近似于上模半径。当然,无论是取固有半径还是上模半径,产品的最终成形半径还要考虑与材质、板厚、下模开口等因素有关的回弹量问题。通常情况下,成形件的最后成形半径会比理论值偏大。
⑴下模的选用。
数控折弯机折弯的工作压力一般可以根据板材厚度、模具开口宽度、材料抗拉强度估算,当开口距越大,所需工作压力则越小;开口距越小,则折弯力矩也越小,因而所需的压力越大。折弯半径与下模开口也有着密切的关系,下模开口宽度改变,则折弯半径随之改变。小开口距产生的半径较小,大开口距产生的半径较大,回弹量随之增大。另外,板料折弯是弹性变形与塑性变形共存的过程,在折弯过程中,会存在一定的弹性变形,外力去除后,工件会有一定程度的回弹,对于大开口下模来说这种现象更为明显。因此折弯下模的选择原则是:确保板料压形时最短边的折弯位置大于下模开口的一半且折弯时不开裂,工作压力符合机床要求的情况下,尽量选用小开口的折弯下模。但对于很薄板材,而零件内弧半径又很大的配件来说,需要大开口的压型下模才能避免压型时材料被挤伤。
对于抗拉强度较高的板料,则模具开口至少应10倍于板厚,这样不仅能确保折弯力,更能增大弯曲半径以减少折弯层断裂的可能性。
⑵上模的选用。
对于数控折弯机来说,确定了下模后上模的选用就显得容易了。上模的大小并不对工作压力起作用,而且对于间隙折弯来说,上模的角度并不会影响零件成形后的角度。只有上模半径大于下模的固有半径时,上模的半径才会起作用。因此可根据下模估算的固有半径及零件的内弧半径选用上模。若所选下模的固有半径小于零件的内弧半径,需尽量选择比零件内弧半径小1~2mm,或等于零件内弧半径的上模。
零件折弯工艺性分析及工艺问题处理
槽形件的折弯工艺性分析及问题处理
⑴工艺性分析。
实际生产中,因机床本身和模具的结构特点,常会碰到一些,如图3所示的槽形件(其中c≥b),不能判断折弯时是否会与上模或机床产生干涉的问题。为了能够对此类槽形件工艺性进行快速判断,结合压型上模和机床的外形,我们进行了一系列的分析与计算。例如:图4为鹅颈形上模第一段的截面示意图,a的最大值为a1max。同理,可得出所有压型上模和机床各段(图5)对槽形件尺寸a、b的要求及a、b关系式。通过这些,不仅可以成功解决以往只能依靠现场模拟判断槽形件工艺性的问题,而且可以让技术人员随时、随地进行槽形件工艺性的快速分析。此外,它也为实现计算机自动判断工艺性提供了理论依据。
' fill='%23FFFFFF'%3E%3Crect x='249' y='126' width='1' height='1'%3E%3C/rect%3E%3C/g%3E%3C/g%3E%3C/svg%3E)
图3 槽形件
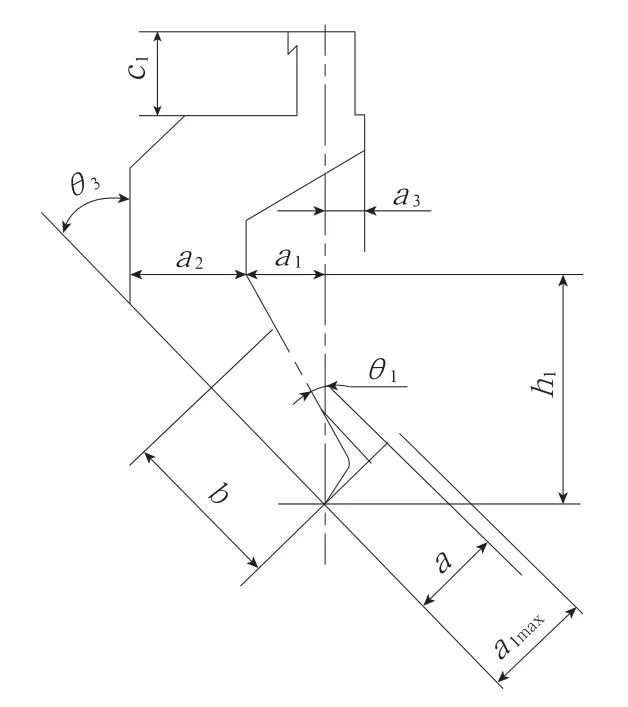
图4 鹅颈形上模截面示意图
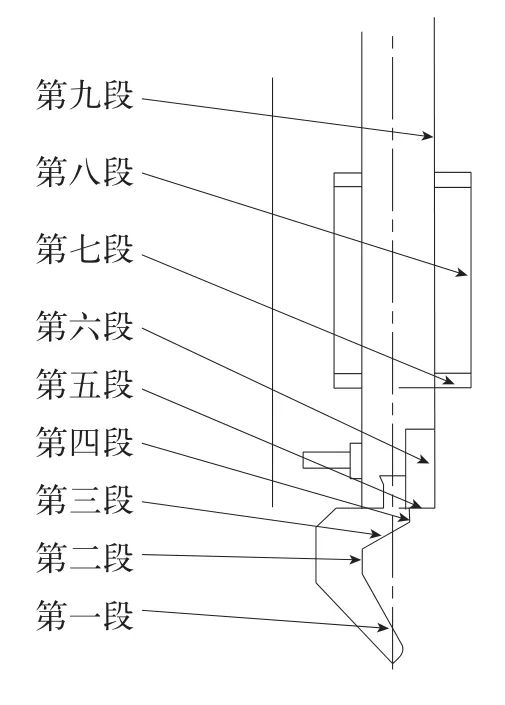
图5 压型上模和机床截面分段图
⑵特殊槽形件的处理。
不满足a,b关系式的槽形件,不能采取正常工艺成形。当零件受载荷强度要求不高时,可采取预弯成形工艺。预弯的角度ψ如图6a所示,通过分析零件截面外形和上模截面形状获得,且越大越好。采用这种成形工艺可避免制作新模具,大大降低生产成本。如图6c所示配件,实际生产中与机床发生了干涉,经用户单位同意,采用预弯成形工艺,该配件才得以顺利制作,其成形过程如图6a、图6b、图6c所示。
' fill='%23FFFFFF'%3E%3Crect x='249' y='126' width='1' height='1'%3E%3C/rect%3E%3C/g%3E%3C/g%3E%3C/svg%3E)
图6 槽形件预弯成形示意图
长、大、厚零件的折弯工艺性分析及问题处理
根据实际生产情况来看,长、大、厚成形件常常会出现压形开裂、船形、鼓肚子等问题。其中,开裂和船形是最为常见的两种问题。下料前充分考虑零件的工艺性往往能从根本上控制这些问题。
⑴压型开裂。
压型开裂常常发生在压型区域的两端,特别是压型线靠近缺口、板又较厚时这种现象极为常见。对于5A06-0铝材的压型,此类问题更是突出。根据现场经验,有以下几种途径可以较为成功地控制这类问题:
1)下料时按压型线垂直于材料纹理方向进行下料,特别是对于5A06-0铝材的压型,尤其要注意。
2)将压型部位两端打磨成圆弧,并精整以降低直角所带来的应力集中。
3)普通钢材可在压型两端采用火焰加热,温度控制在750℃左右,即钢板颜色变成“樱红色”时再进行折弯。
4)16Mn低合金结构钢对缺口较敏感,拉伸时极易开裂,设计时应尽量将缺口偏离折弯线。
5)当零件的折弯线处于宽窄交界处时,为了使弯曲时易于变形,防止交界处开裂,通常在弯曲宽窄处增添止裂孔。当折弯相对半径很小时,为防止弯曲端部开裂,在弯曲端部增添止裂孔。
6)5A06-0类的铝材设计时应尽量取较大的半径。
⑵船形。
长、大、厚零件在下料后会存在较大的内应力。特别是火焰下料的配件,还会存在一个热影响区。此时在热影响区板料的纤维收缩变短,而在板料的中间纤维伸长。压型受力打破了原有的平衡,内应力很快便释放出来,成形出来的零件也就出现了船形。因此在成形前对板料进行应力释放是控制船形问题的关键。采用工艺放量,下料后使用平板机进行反复平板,一方面消除切割带来的变形,另一方面可消除内应力;然后再将工艺放量进行刨边去除。生产中可能还会在加工后出现内应力不平衡的情况,如SS9型机车底架梁体在进行平板、刨边、刨坡口进行压型后便出现了这类问题,而且尺寸偏差较大,经分析确定是加工后产生了较大的内应力,采用加工后再增加一道平板的工序后,问题解决了。另外对于这种情况在成形时,可以通过适当地加大压力,减少回弹,延长压型时间、保压以减少应力的释放进行控制。
弯曲力矩偏小的工艺处理
在进行折弯工艺分析时,必须考虑零件的弯曲力矩。为保证足够的弯曲力矩,根据板厚对压型边高≤5t的边需进行放量折弯(板越厚需要的压型边高越长)后再去除放长量。
数控折弯机成形工艺存在的不足
尽管数控机床通过程序控制来折弯板料,但是因为数控机床本身的精度和加工材料的误差,并不能保证得到满意的折弯角度。在折弯过程中通过各种操作速度使板料得到所需的折弯角度,或调整上模伸入下模的开口深度得到所需的折弯角度时,都应尽可能使用量角器或样板进行检测,直到角度达到要求为止。实际成形中材料性质、变形速度等都可能影响材料的折弯成形性,另外板厚误差也严重影响了展开料的计算,因此很多时候还得采用误差跟踪或试验的方法进行修正。
结束语
随着数控折弯机工艺日渐成熟,折弯产品质量有了很大的提高,确保了我公司DJ4型机车的顺利制作,并为更好机型的机车制作提供了有力保障。
——摘自《钣金与制作》 2015年第6期